Ultrasonic
Spiral Weld
Ultrasonic testing System
Ultrasonic testing of DSAW/SAW welded spiral pipe is a well-established and widely used technique, which is used to meet API and other codes of practice. InspecTech offers comprehensive systems for Spiral Weld testing, including an automated, laser guided weld tracking subsystem.
InspecTech has developed and refined a probe system that utilizes immersion transducers in a special transducer holder. This system creates shear waves at the pipe interface. With multi-channel processing technology, InspecTech’s multi transducer probe assemblies are easy to set-up and calibrate.

Key Feature
Multi probe test heads are easy to set-up and calibrate.
​
Tandem probes offered to ensure full cross-section testing.
​
Flexible scope of supply with a wide variety of options.
​
Instant recall of previously used setups.
​Complete data logging provides accurate records of all test parameters and test results.
Robust mechanical construction.
Complete Data Logging of all on-line Test Parameters easily stored, retrieved, hard-copied or downloaded.

Our laser guided tracking system is used for spiral tube weld testing the tracking system is very reliable and simple to set-up. Operator needs to position the test head in desired location on the weld and engage the tracking system. From this moment on the test head will automatically follow the weld, even with significant weld line shift over time.
The configuration of the system and scope of supply can be individually adjusted. Based on mill structure and testing requirements the best and most cost effective option will be offered by InspecTech to meet our customers’ needs.
ON-LINE
Ultrasonic testing System
Over the years the welded tube industry has come to rely on InspecTech® ultrasonic testing systems to verify weld quality and integrity both on the tube mill and on the finishing floor. Ultrasonic testing of welded tube is a universally recognized method, offering equal sensitivity to both inside and outside defects regardless of material thickness.
Codes of practice such as ISO, API and CSA all cite ultrasonic testing of welds as an acceptable, or even mandatory, method. Depending upon requirement, InspecTech can supply systems with 2, 4, 6 or more transducers to test various material thickness ranges and also to test HAZ (heat affected zones) and monitor material gauge.
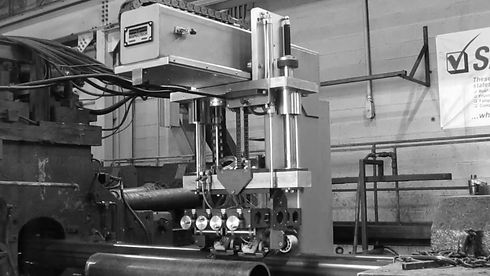
Key Feature
Advanced transducer technology.
Multi-probe test heads are easy to set-up and calibrate.
Ideal for inspecting to API-5L, API-5CT and ISO standards.
Robust mechanical construction.
Complete Data Logging of all on-line Test Parameter data is easily stored, retrieved, hard-copied or downloaded.
Instant recall of previously used setups.

With many years of experience in NDT systems, InspecTech exercises continuous improvement policies, to supply the welded tube industry with systems of the highest reliability and sophistication, coupled with ease of understanding and operation.
For weld-line testing of carbon steel tubing 50mm (2.0”) diameter and up (and more recently down to much smaller diameters), the method of choice is ultrasonic testing. Ultrasonic testing is very sensitive to defects throughout the weld section and, at the same time, the test is relatively insensitive to process variations.
Included accessories
Advanced transducer technology.
Multi-probe test heads are easy to set-up and calibrate.
Ideal for inspecting to API-5L, API-5CT and ISO standards.
​Robust mechanical construction.
Complete Data Logging of all on-line Test Parameter data is easily stored, retrieved, hard-copied or downloaded.
Instant recall of previously used setups.
OFF-LINE
Ultrasonic testing system
InspecTech® Off-Line Ultrasonic Test Systems are specially designed and configured to inspect the entire length of a weld seam in a tubular product.
This form of testing is normally required for code compliances such as API and ISO. Testing is similar to InspecTech’s On-Line Test System, but the test head is configured differently and more mechanization is required.

Key Feature
Multi-probe test heads are easy to setup and calibrate.
​
Ideal for inspecting to API-5L, API-5CT and ISO standards.
​
Individually engineered units to meet specific NDT requirements.
​
Flexible scope of supply with a wide variety of options.
Complete Data Logging of all Test Parameters Easily stored, retrieved, hard-copied or downloaded.
​
Discrete Array technology optional.
​
Optional end-zone testing.
​
Multiple test heads available to enhance productivity.
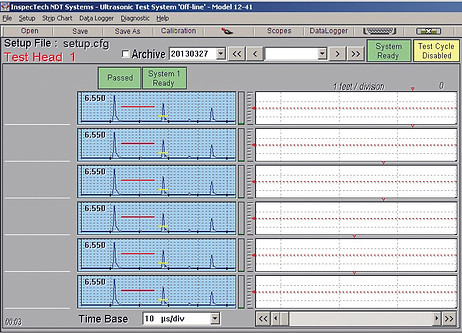
This test unit uses an overhead carriage, which travels above a stationary pipe. This arrangement is the usual method of choice.
​
An alternative method, involving a stationary test head with the pipe being conveyed underneath is also available.
Skelp
Ultrasonic monitoring system
The InspecTech® Ultrasonic monitor for pipe skelp or strip material is a multi-channel unit that measures and records material gauge as well as checking for laminations and segregations in the material.
The monitor is used in pipe and tube manufacture as well as in plate and strip mills.

Key Feature
Coverage from 10% to 100% of material surface.
Unused transducers can be “parked” to suit different strip widths.
Alarm function can be tailored to defect size or area.
Outer transducers can be set up to follow strip edges.
Complete Data Logging of all on-line Test Parameters easily stored, retrieved, hard-copied or downloaded.
Instant recall of previously used setups.

To accommodate different widths of strip or skelp, transducer arms can be positioned individually on a crossbar that straddles the line. Unused transducers are simply lifted into a “park” position, and they become inoperative when parked.
​
Undulations and twists in the tested material are compensated by the individual transducer holders, which include both pivot and swivel actions. In addition, bouncing of the transducer arms is minimized by a pneumatic system that applies constant downward force to the test heads.
IBIS
Scarf monitoring system
The InspecTech® I.B.I.S. (InspecTech B-Scan Inspection System) is an ultrasonic device that is especially useful to the welded tube industry. The I.B.I.S. scans the weld zone, and monitors the quality of the flash removal process.

Key Feature
Scrap Reduction. Catch flash removal problems before they become costly.
Real Time Presentation of wall thickness data in engineering units over the weld.
Audio and visual alarms for high and low limits of wall thickness.
“Hands Free” unattended operation
Complete Data Logging of all on-line Test Parameters easily stored, retrieved, hard-copied or downloaded.
Instant recall of previously used setups.
Weight Calculation and Cutting to Weight (Optional).

The I.B.I.S. is primarily a scrap reduction tool. It displays the weld profile in engineering units and in real time on a video display. Broken, worn or chipped flash cutting tools or mismatched weld edges are easily detected and alarmed. The I.B.I.S. will also monitor weld profile to make sure that the overall weld thickness is within tolerance.